Auto
Yamaha Motor Launches Premium High-Efficiency Dual-Lane Modular YRM20DL – Reduces Transport and Head Standby Loss
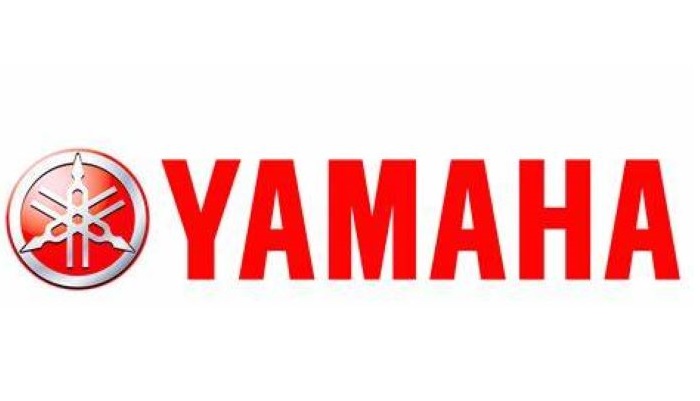
Yamaha Motor Co., Ltd. (Tokyo:7272) announced that the new YRM20DL surface mounter*1 will be launched on April 3, 2023.
The YRM20DL is a premium high-efficiency modular that achieves improved actual and per-unit-area productivity with a newly developed high-rigidity dual-lane conveyor by further reducing transport losses etc. YRM20DL is built on the basic performance of the company’s flagship high-speed, high-accuracy, high-versatility, universal mounter YRM20.
YRM20DL supports a maximum PCB width of up to 330mm where the same width PCB is being conveyed at the front and rear while in dual-lane production mode. In the case of parallel mounting, the front and rear heads can operate without any interference up to a maximum PCB length of 380mm, enabling high-efficiency mounting without loss.
Furthermore, the basic performance of the unit has been further enhanced to achieve an overwhelming productivity of 120,000 CPH*3 (under optimal conditions)*2, the world’s highest level of speed in its class, along with a higher-accuracy placement of ±15µm (Cpk≥1.0) through the revision of the layout such as bringing the mounted components pick-up area and the mounting area closer together, optimizing the main spindle motion control, improving the rigidity of the conveyor and the corrective functionality etc., enabling the unit to achieve an overwhelming productivity of,.
Yamaha Motor has realized the ideal concept of a 1 STOP SMART SOLUTION by taking advantage of the company’s strengths as a full-lineup manufacturer of mounting equipment, including surface mounters, printers, dispensers, and inspection systems. The company promotes the Intelligent Factory system, which comprehensively realizes higher efficiency in the mounting process through smooth and advanced inter-equipment cooperation without black boxes.
*1: Surface mounters: Production equipment designed to mount various electronic components onto PCB’s (Printed Circuit Boards), which are then incorporated into electronic products.
*2: Comparative mounting capacity (CPH) under optimal conditions for surface mounters in the 2-Beam, 2-Head Class. Yamaha Motor survey, February 01, 2023
*3: CPH (Chips Per Hour): Total number of chips that can be mounted per hour (unit time). Indicates processing capacity under various conditions.
Market Background and Product Outline
In addition to the rapid electrification of powertrains for in-vehicle electronics, the miniaturization, high-densification, high functionality, and diversification, as well as shortened product cycles have increasingly accelerated for a variety of products such as appliances, personal computers, and mobile telephones. In response to this, the miniaturization of components have also progressed, and higher-performance, higher-efficiency equipment with greater flexibility and efficiency has been introduced, promoting a dramatic increase in production capacity at manufacturing sites. However, along with improvements of these throughputs, the ratio of fixed-value losses that do not generate value, such as transportation time to production time, have also come into focus.
Yamaha Motor has therefore newly developed the YRM20DL, a dual lane version of the YRM20 which is the latest flagship mounter to adopt the new generation platform. The unit supports various dual-lane production methods, such as transporting two PCBs of the same type by parallel mounting, transporting two PCBs of different types, and alternate mounting, making it possible to select and operate the optimal production system for each product PCB type. As a result, fixed-value losses such as transport losses can be greatly reduced in a wide variety of SMT production lines, from high-speed mass production to high-mix low-volume production, along with improved actual productivity and per-unit-area productivity.
■ Mounting example using dual lanes (Arrows indicate movement of the head)
1) Achieves higher speed and higher accuracy through improved basic performance
By revising the dynamic layout, the unit has achieved the world’s highest level of 120,000 CPH in its class (under company optimum conditions) realizing overwhelming productivity. This has been achieved by way of minimizing the movement distance by bringing the pickup and mounting areas closer to each of the two heads, and further optimizing the overall spindle motion control.
High-accuracy mounting of ±15 μm (Cpk≧1.0) is achieved by increasing the rigidity with the newly developed conveyor and improving the correction function. The RM head/HM head supports 0201 (0.25 x 0.125 mm) sized ultra-small chip component mounting and narrow adjacent mounting.
2) Adoption of a newly developed dual-lane conveyor that reduces transport loss and improves per-unit-area productivity
The newly developed high-rigidity dual-lane conveyor supports a maximum PCB width of up to 330mm where the same width PCB is being conveyed at the front and rear while in dual-lane production mode. An ultra-high-speed rotary RM head that employs overdrive motion (mutual head insertion) allows the front and rear heads to operate without any interference up to a maximum PCB length of 380mm, enabling highly efficient mounting without head standby loss.
In single-lane production, which uses only one of the two lanes, it is possible to transport PCBs up to a maximum length of 810mm, a maximum width of 610mm, a transportable weight of 3kg, and a maximum PCB thickness of up to 6.5 mm. This new model is also compatible with a wide range of extra-large-sized PCB’s, jig conveyance, etc., including for automotive products, industrial, medical, power devices, and LED lighting.
3) Other key features
Head can be selected from 3 types
– Ultra-high-speed rotary RM head with overdrive motion
– In-line HM head that combines high speed and high versatility with “1 head solution” that can handle ultra-small chip components to larger components with one type of head
– In-line type FM head capable of handling tall and odd-shaped components
Supports various labor-saving functions
– Auto-loading feeder that can easily replenish tape components at any time without the need to stop production
– eATS30, a non-stop tray supply device that can supply tray components in units of pallets/magazines without the need to stop production
– Non-stop loading/unloading feeder carriages that enables setup work for feeder carriages replacement without the need to stop production on one lane
– Automatic exchange of push-up pins, greatly reducing workloads when changing products
Integrity and ease of maintenance
– Nozzle ID management that enables maintenance optimization according to the number of accumulated shots
– Self-diagnostic and self-recovery functions maintain a clean state, allowing continued high-quality production nozzle health care/feeder maintenance warnings

-
Auto2 years ago
Honda Marine Debuts All-New BF350 Outboard Company’s First V8 Motor Available Commercially, Flagship Model Offers Premium Power and Unparalleled Performance for Extraordinary Boating Experiences
-
Auto2 years ago
New Features Further Increase Desirability Of Bentayga Range
-
Technology2 years ago
Oracle Partners with TELMEX-Triara to Become the Only Hyperscaler with Two Cloud Regions in Mexico
-
Auto2 years ago
Honda and Acura Electric Vehicles Will Have Access to Largest EV Charging Networks in North America Aided by New Agreements with EVgo and Electrify America
-
Lifestyle2 years ago
2023 Nike World Basketball Festival Brings the Best of Basketball Style, Culture and Community